Large 3D metal printer deployed in bush trial
Share the post "Large 3D metal printer deployed in bush trial"
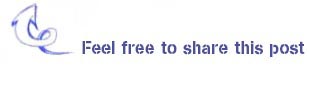
In a world-first, a ‘WarpSPEE3D’ 3D metal printer was deployed and put through its paces by the Australian Army during a field exercise in the Northern Territory this week.
CAPTION: A WarpSPEE3D 3D printer deployed at Mount Bundey Training Area, NT. Photo by Petty Officer Peter Thompson.
The successful trial demonstrated the potential for this cutting-edge metal 3D printing technology to be deployed to the field by the Australian Defence Force.
WarpSPEE3D is the world’s first large-format metal 3D printer to use patented cold-spray technology that enables significantly faster and more cost-effective metal part production than traditional manufacturing.
Developed by SPEE3D, Australian award-winning manufacturer of metal additive manufacturing technology, the printer is capable of printing large metal parts up to 40kg at a record-breaking speed of 100grams per minute.
The printer arrived in Darwin in early June and, little over a week after being installed at the Australian Army’s Robertson Barracks, soldiers from the 1st Combat Service Support Battalion (1CSSB) packed up and trucked the printer out bush to take part in a three-day trial at the Mount Bundey field training area, 120km south-east of Darwin.
During the three-day trial, the WarpSPEE3D was manoeuvred to various bush locations and unloaded on different terrains.
The printer was unloaded and operational – ready to print – within 30 minutes and the printer produced a variety of parts.
SPEE3D printers make metal parts the fastest way possible, leveraging metal cold-spray technology to produce industrial-quality metal parts in just minutes, rather than days or weeks.
This process harnesses the power of kinetic energy, rather than relying on high-power lasers and expensive gasses, allowing 3D metal printing in the field, at affordable costs.
The Australian Army announced a $1.5 million investment in a pilot of SPEE3D technology in February 2020 with a 12-month trial designed to test the feasibility of deploying 3D metal printers both on base and in the field.
SPEE3D partnered with the Advanced Manufacturing Alliance (AMA) and Charles Darwin University (CDU) to deliver the program with soldiers from the Australian Army 1st Brigade training in 3D printing at CDU since February.
The program aims to significantly increase the availability of unique parts to the Army compared to what the regular supply chain can provide.
SPEE3D CEO Byron Kennedy said the first field deployment of WarpSPEE3D was an important milestone for SPEE3D.
“While our equipment was initially designed for industrial use, this trial proved that our equipment is actually very robust and can endure harsh conditions and rough handling very well,” Mr Kennedy said.
“We look forward to future exercises and continuing to learn how we best serve the Australian Army and defence industry.”
1CSSB Commanding Officer Lieutenant Colonel Kane Wright said the year-long trial was progressing well considering the adjustments to training [caused by COVID-19].
“This phase has seen the 3D printing capability deployed to the field, alongside vital military equipment, contributing to the mission during this training cycle,” Lieutenant Colonel Wright said.
“The ability to print repair parts in an environment like this has the potential to significantly reduce our footprint and repair damaged equipment, on the spot, to get us back to our main priority.”
.
.
.
.
.
.

.
.
Share the post "Large 3D metal printer deployed in bush trial"
Here is a thought. Build a bigger one and print submarines…
What parts? Is there quality control? Design experience? What correct technical information can a solder obtain in the field? This why we have design authorities in Melbourne to prevent unsatisfactory materiel. A printed part is never a replacement for genuine parts. This has a lot of legal problems if someone is injured due to a printed part failing.