Army starts field-trial of 3D parts printing
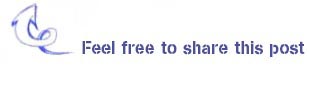
Army has kicked off a 12-month trial of 3D metal printing that could see on-the-spot design and manufacturing available to soldiers deployed on operations.
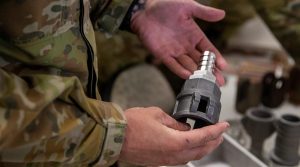
CAPTION: Australian soldiers from Darwin-based 1st Combat Service Support Battalion are receiving instruction on the capabilities of SPEE3D printing. Photos supplied.
The trial is already underway in partnership with SPEE3D and Charles Darwin University (CDU) – the same company and technology recently engaged by the Royal Australian Navy.
The $1.5 million venture recently announced by Minister for Defence Industry Melissa Price will see 20 Darwin-based soldiers trained in advanced additive manufacturing.
Mostly drawn from 1st Combat Service Support Battalion (1CSSB), the soldiers are already being taught how to design and print parts using the WarpSPEE3D 3D metal printer.
This trial represents the realisation of a 1CSSB proposal to Army in 2019, to modernise and enhance the resilience of the ADF’s supply chains.
Commanding Officer 1 CSSB Lieutenant Colonel Kane Wright said that the initiative demonstrated how Army was keeping up with the accelerated nature of warfare.
“This partnership with CDU and SPEE3D shows that we as an army are looking to the future and embracing advanced technologies to speed up our processes,” Lieutenant Colonel Wright said.
“At maturity, we see it becoming an essential enabler that will redefine how logistics is employed to support our dependencies on the future battlefield.”
Lieutenant Colonel Wright said the printer harnessed the power of kinetic energy to fabricate parts in a safe and environmentally friendly manner, allowing 3D metal printing in the field.
“This will reduce the requirement to deploy with bulky holdings of multiple repair parts, hence increasing mobility and survivability and reduce time waiting for new parts to create greater resilience in the supplychain,” he said.
Initial soldier training will be delivered at CDU’s Casuarina Campus by experienced researchers over a 10-week period.
Weekly sessions will cover everything from the fundamentals of design, 3D modelling and printing, to the testing and evaluation of developed parts.
Lieutenant Colonel Wright said that the Army would begin by trialling the production of non-safety-critical repair parts while leaning on industry experts to explore the full potential of the capability.
Among the 20 Darwin-based soldiers already being trained on the WarpSPEE3D 3D metal printer, Lance Corporal Sean Barton was quick to volunteer for the trial.
“This is a very exciting opportunity for me and very different from my regular trade as a fitter,” Lance Corporal Barton said.
“I am looking forward to getting my hands on the software, learning about the design process and being one of the first to learn how to use the technology – it’s pretty cool,” he said.
How supply soldiers will see themselves with SPEE3D technology 😉
The Royal Australian Navy launched a similar trial in November last year, together with SPEE3D and CDU, to streamline the maintenance of patrol vessels.
.
.
.
.
.
.

.
.